YAW-5000R microcomputer controlled electro-hydraulic servo p
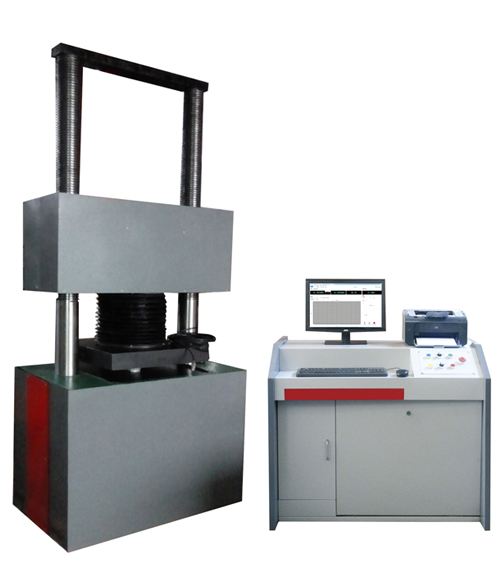
Product name: YAW-5000R microcomputer controlled electro-hydraulic servo pressure testing machine
Product introduction
1. The host of YAW-5000R microcomputer controlled electro-hydraulic servo pressure testing machine adopts single-rod plunger-type cylinder to apply the test force, and uses microcomputer to control multi-stage hydraulic loading, continuous loading stability, multi-stage test force holding, automatic collection and storage of data, and drawing of curves; it supports automatic printing of test reports, and uses the computer to timely control the test process, display the test force and test curve, with easy and reliable operation, being easy to operate. It adopts high-precision directly force-measuring cylinder-type sensor and proportional servo valve element, and it has multiple (closed loop) control modes, including constant load, constant stress and constant displacement, making the performance of the whole machine being stable and reliable.
2. This machine is mainly used for performance tests testing the compressive mechanical property and other properties of metallic and concrete specimens, and it satisfies the requirements of such standards as GB/T2611-2007 General Requirements for Testing Machines, JJF1103-2003 Evaluation for Computerized Data Acquisition Systems of Universal Testing Machines, JJG139-1999 Verification Regulation of Tension, Compression and Universal Testing Machines, GB/T 3159 -2008 Hydraulic Universal Testing Machines, GB/T16826-2008 Electro-Hydraulic Servo Universal Testing Machines, and GB/T50081-2002 Standard for Test Method of Mechanical Properties on Ordinary Concrete, and it can complete the axial compression test.
3. YAW-5000R microcomputer controlled electro-hydraulic servo pressure testing machine is a necessary testing device for measurement and detection, scientific research institutes and institutions, manufacturing enterprises, road, building, railway and bridge construction units and supervision companies and quality inspection departments.
Hydraulic system
The hydraulic principle is load-adaptive oil-inlet throttling speed-regulating system.
The hydraulic oil in the oil tank enters the oil circuit via the high-pressure oil pump driven by the motor, and it flows through one-way valve, high-pressure filter and proportional servo valve and enters the oil cylinder. The high-precision oil pressure sensor is mounted on the oil cylinder piston, and it converts force signals into electrical signals and transmits to the computer, and the computer collects and processes them and converts them into test force values, and displays them; meanwhile, the computer gives control signals to the servo valve according to the signals of sensor and the compilation of control programs and controls the opening size and direction of servo valve to control the flow of oil cylinder and realize such servo control as constant-rate load, constant-rate stress, constant-rate displacement, load holding and displacement holding; the cooler adopts the air cooling device, and the power of the whole machine is 5KW.
Microcomputer system
The system adopts EHC-3100 electro-hydraulic servo measurement and control box researched and developed by our company, servo valve group and Testpuye measurement and control software which constitute the measurement and control system of electro-hydraulic servo pressure testing machine; the measurement unit adopts high-precision pressure sensor and drawing displacement sensor, and it can realize load closed-loop and displacement closed-loop control over the pressure testing machine, having such features as high control precision, strong adaptability and good long-term stability.
1. Adopting microcomputer control display system, completing the setting of test parameters, control, data collection, processing and analysis, storage and display during the test process, with precise and accurate control and measurement.
2. Being equipped with win7 system special software for the testing machine, which can be used for statistics and process, and output and print various required test curves and test reports, being equipped with such functions as test curve enlargement, comparison and traversal, being intelligent and convenient.
3. Self-built powerful test database, which makes it possible that the test data can be saved, inquired and called at any time, and realizes the data transmission and conversion with the user LAN and Internet.
4. Being provided with two-channel full-automatic closed-loop measurement and control function, making the operation being direct, fast and high-efficiency.
A. Adopting the PID control strategy to realize the closed-loop control of load, which can realize such functions as constant-rate loading, load holding and constant-rate unloading, with the loading speed set freely;
B. Adopting the PID control strategy to realize closed-loop control of displacement, which can realize such functions as constant-rate displacement control and displacement holding, with the displacement speed set freely;
5. Full-automatic control of test force and travel speed, realizing compression tests of concrete and other materials.
6. If adding auxiliary appliances, it can complete bending, compression and shear test items of many other materials
7. Local test interface:
A. This machine adopts high-precision sensor and digital control valve, microcomputer full-automatic control, automatic testing of shape breaking.
B. Full Chinese interface, easy to operate, visual display of interface: such display units as force value, peak value, loading speed fluctuation, force and time curve, which test block of the group at present, and countdown of interval time.
Main program interface
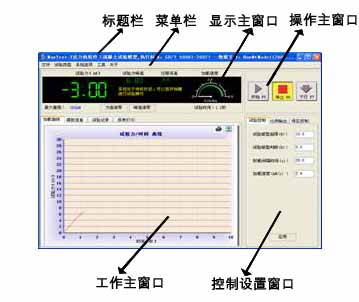
C. Being provided with the database for laboratory networking, and in the case of networking, data can be directly extracted from the database, without change of software or host part.
D. As for the format of statement, the form can be designed according to users’ requirements, and it is provided with special form template writing software, which has been installed in the machine.
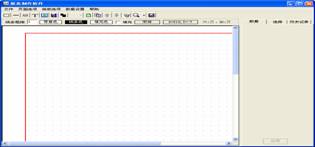
E. The form is provided with a manual filling box, and the external conditions of current test can be reflected in the statement.
8. Having a printer to print test reports;
9. Having a complete safety protection device:
A. When the test force exceeds 2%~5% of the maximum test force of each grade, overload protection, system load;
B. When the piston displacement reaches the limiting position, travel protection, oil pump motor stops;
Main technical performance parameters
1. Maximum test force: 5000kN
2. Measurement range of test force: 4%~100%F.S;
3. Accuracy of test force: ±1%;
4. Accuracy class of the whole machine: Class 1
5. Force measuring mode: Measured by high-precision pressure sensor;
6. Accuracy of sensor: 0.1%FS;
7. Travel of piston: 0-150mm;
8. Maximum test (distance between upper and lower pressing plates) space: 500mm; (adjustable)
9. Distance between columns: 500mm;
10. Dimension of upper and lower pressing plates: 510×410mm (the base is marked with round line and cross line, which are convenient for the centering and locating of specimen);
11. Measurement range of displacement: 150mm
12. Displacement resolution: 0.001mm
13. Accuracy of displacement indication: ±1%
14. Control range of constant-rate stress: 1-10N/mm2·S-1
15. Control error of stress rate: ≤±5%
16. Control and adjustment range of displacement rate (telescoping rate of oil cylinder):50mm/min
17. Control error of displacement rate: ±1%
18. Control and adjustment range of strain rate: 0.00025~0.0025/s
19. Control error of strain rate: ±5%
20. Motor: AC380V±10% 2KW;
21. Weight of host: Approximately 2,700kg
22. Hydraulic loading, microcomputer servo automatic control, sensor measurement, OSD (on screen display).
23. Load holding function: Having load holding of high-precision proportional servo valve, making multi-level control of axial test force.
Adopting low-damp combined sealing elements, test force holding stability and reliability.